Detail Author:
- Name : Mazie Stamm
- Username : jada57
- Email : vdubuque@gmail.com
- Birthdate : 1987-05-23
- Address : 5335 Cummerata Dale Apt. 786 Friesenton, MT 35913
- Phone : 818-476-5257
- Company : Gutkowski, Schaefer and Wilkinson
- Job : Precision Lens Grinders and Polisher
- Bio : Quia eum cumque vel. Ullam consequuntur perspiciatis et omnis aut minus aliquid. Et dolore exercitationem autem natus possimus ipsa.
Socials
instagram:
- url : https://instagram.com/agustina_koch
- username : agustina_koch
- bio : Minus ut nostrum non ut exercitationem. Sequi reprehenderit reiciendis quia accusamus occaecati.
- followers : 993
- following : 2889
linkedin:
- url : https://linkedin.com/in/koch2025
- username : koch2025
- bio : Harum voluptatibus officiis ex sapiente.
- followers : 5576
- following : 2409
facebook:
- url : https://facebook.com/kocha
- username : kocha
- bio : Consequatur labore corporis et aut perspiciatis accusamus quia.
- followers : 3252
- following : 2245
Creating things from earth's own materials has been a human activity for a very, very long time. This old way of making useful and decorative items, often by heating clay to make it firm and lasting, is something people have done for thousands of years. From simple bowls to elaborate works of art, the act of forming clay and then making it strong through fire has always been a core part of human expression and daily living, you know. It’s a process where simple earth becomes something quite special, more or less.
When we talk about pottery, we're really looking at a craft that takes natural substances, mainly clay, and shapes them into all sorts of things. These things are then put through a heat treatment, making them very tough and ready for use. My text mentions that pottery is about shaping vessels and other items from clay and other raw elements, which are then heated at high temperatures to give them a hard, lasting form. It's a method that has been around for ages, one of the earliest and most widespread forms of art that involves shaping clay and making it firm with warmth. People have used this skill to make items that are commonly quite helpful, like containers for food or water, or just pretty things to look at, as a matter of fact.
In studios, like the one in Woodstock, Vermont, where every piece of pottery starts with skilled hands and a genuine affection for the craft, the journey from soft clay to a finished piece is quite interesting. Whether someone is learning to use a spinning wheel, or just looking at what's on display, the essence of this making process is always there. My text also points out that pottery is essentially ceramic materials, including common types like earthenware, stoneware, and porcelain. To be truly called pottery, an item must have gone through a firing process. It’s the art of shaping clay and then heating it intensely in a special oven, often called a kiln. The very place where these items are made by a person who works with clay is also called a pottery. The end result is something truly unique, you see, something that holds its shape and purpose for a long, long time. This is where new methods, like pottery tray foam pressing, come into play, offering fresh ways to create these items, actually.
Table of Contents
- What is Pottery, Really?
- The Heart of Making Pottery
- Why Think About Pottery Tray Foam Pressing?
- Getting Started with Pottery Tray Foam Pressing
- How Does Pottery Tray Foam Pressing Work?
- Making Your Mark with Pottery Tray Foam Pressing
- What Can You Create with Pottery Tray Foam Pressing?
- Tips for Better Pottery Tray Foam Pressing
What is Pottery, Really?
When we talk about pottery, we are discussing a very old and widespread way of making things. It's about taking clay and other natural materials, then shaping them into containers or other items. These items are then put into a very hot oven, which makes them tough and lasting. My text says that pottery is one of the oldest forms of decorative art, made from clay and made hard by heat. The items made are usually quite useful, you know, like plates or cups. It's basically a method of using clay and other raw stuff to give shape to containers or other objects. These are then put through very high temperatures, which changes them for good. It's pretty much a craft that involves shaping clay and other ceramic materials, then heating them to a very high degree in a kiln. The final item is something that can be used for many things, or just enjoyed for its look. This practice has been around since people first needed containers for their daily lives, and now it's enjoyed as a creative pursuit, too it's almost a bridge to our past.
Pottery is made up of ceramic materials, covering major kinds of pottery items such as earthenware, stoneware, and porcelain. For something to be considered pottery, it absolutely must have been fired. It's the skill of shaping clay and making it hard by heating it in a kiln. The place where these items are made by a person who works with clay is also called a pottery. The finished piece is what we see and use. It’s a craft of shaping clay and other ceramic materials. You can find out about the tools and methods used in pottery, as well as get ideas for your own creations. My text mentions that pottery is a craft that involves kneading clay, giving it a shape, and then firing it. It has a long history, developing because people needed containers for their daily lives. Now, it's something people enjoy making for fun and beauty. It’s interesting to think that pottery was the very first human-made material, in a way. The word refers to items made of clay that have been given a desired shape, dried out, and then either fired or not. These items are often quite useful, and they are heated at high temperatures to achieve their lasting form, you see. Whether you're at a workshop learning to use a wheel, or just looking around a shop, the core process remains the same. The items can be made using electric, gas, or wood kilns. They are made from things like kaolin and feldspar, which are specific types of clay and minerals. The term really just means items made of clay that have been shaped, dried, and then made hard by heat.
The Heart of Making Pottery
At its core, making pottery is about a connection with the earth itself. You start with something soft and pliable, a bit like thick mud, and through your hands, you give it a new purpose. This process, as my text describes, involves forming vessels and other objects. It's an old way of doing things, one that has been passed down through many generations. The simple act of shaping clay, feeling it change under your touch, is deeply satisfying. It's a slow process, in some respects, one that asks for patience and a gentle touch. The clay itself, made of various natural materials, holds the promise of something lasting. This is where the true spirit of pottery comes alive, you know, in the quiet moments of creation before the heat transforms everything.
The journey of a piece of pottery doesn't end with shaping. It then moves to the part where heat plays a major role. My text makes it clear that these items are fired at high temperatures to make them hard and durable. This firing step is what truly makes clay into pottery. Without it, the clay would simply return to mud if it got wet. The heat changes the clay at a basic level, locking in its shape and making it strong enough to hold liquids or withstand daily use. It's a kind of magic, really, where a soft, humble material becomes something completely different, something that can last for a very long time. This transformation is what gives pottery its lasting appeal and its place in our homes and history. It's pretty fascinating, actually, how such a simple process can lead to such lasting results.
Why Think About Pottery Tray Foam Pressing?
You might wonder why anyone would consider a method like pottery tray foam pressing when there are so many traditional ways to shape clay. Well, sometimes, the usual ways don't quite give you the specific shape or texture you're looking for, or they might be a bit too complex for a certain kind of project. This pressing method offers a fresh approach to creating forms, especially for items that need a consistent shape or a particular kind of surface. It's a way to get a uniform thickness and a smooth finish without needing a lot of specialized equipment or years of practice on a wheel, for example. It’s about making certain shapes more accessible to more people, which is quite appealing, isn't it?
Consider the kind of items you might want to make, like serving trays, platters, or even decorative wall pieces. Achieving a perfectly flat base or a consistent curve can be tricky with hand-building or even on a potter's wheel. Pottery tray foam pressing provides a reliable way to achieve these kinds of shapes with less effort. It helps in getting a nice, even compression of the clay, which can lead to fewer cracks during drying and firing. This means less frustration and more successful pieces, which is always a good thing for anyone making pottery, you know. It also opens up possibilities for creating multiples of the same item, if you happen to be making a set of things, which is pretty handy.
Getting Started with Pottery Tray Foam Pressing
Before you jump into pottery tray foam pressing, it's good to have a few things ready. You'll need some clay, of course, prepared in a way that it's easy to work with – not too wet, not too dry. You'll also need the foam itself, typically a dense kind of foam that can withstand pressure and spring back to its original shape. Think about the size and shape of the tray or item you want to create; this will help you choose the right size of foam and any molds you might use. It's a bit like preparing your ingredients before you start cooking, ensuring everything is in place for a smooth process, you see. Having everything organized from the start can save you a lot of time and effort later on, honestly.
You'll also want to think about what kind of surface you'll be pressing onto. A sturdy, flat board is usually best. Some people use a rolling pin or a special press to apply even pressure. The key here is consistency. You want the clay to be pressed evenly across the entire surface of the foam to get a good, uniform result. It’s not a race, so taking your time to set things up properly is well worth it. This initial setup is quite important for the success of your pottery tray foam pressing project, as a matter of fact. It lays the groundwork for the kind of shape and feel your finished piece will have, so being thoughtful here can really make a difference.
How Does Pottery Tray Foam Pressing Work?
The idea behind pottery tray foam pressing is pretty straightforward, actually. You start with a slab of clay that has been rolled out to an even thickness. Then, you place this clay slab over a piece of foam that has the general shape you want your tray to take. The foam acts as a kind of cushion or a flexible mold. You then apply pressure to the clay, pushing it down into the foam. This pressure makes the clay take on the shape of the foam beneath it. It's a simple mechanical action, really, that allows the clay to conform to a specific form without too much fuss. The foam, being soft, allows for a gentle, even pressure to be applied across the clay surface, which is pretty useful for avoiding thin spots or air pockets, you know.
The process often involves placing a flat board or another piece of foam on top of the clay and then pressing down. This pressing can be done by hand, using your body weight, or with a simple press tool. As the clay is pushed into the foam, it stretches and settles, taking on the contours of the foam. Once the pressure is released, the foam springs back, leaving the clay in its newly formed shape. This method is particularly good for creating trays or shallow dishes that need a consistent base and sides. It’s a bit like using a cookie cutter, but for three-dimensional shapes, allowing for a good deal of precision in your pottery tray foam pressing efforts. This technique helps to achieve a smooth and even surface, which is often a goal for many clay artists, you see.
Making Your Mark with Pottery Tray Foam Pressing
After the initial shaping with pottery tray foam pressing, you can add your own personal touch. This is where the piece truly becomes yours. You can trim the edges, smooth out any rough spots, or add textures and patterns. Some people like to use stamps or carving tools to create unique designs on the surface of the clay while it's still soft. You might add small feet to the bottom of your tray, or create handles for easier carrying. It’s about taking the basic form created by the pressing method and giving it character and individuality. This step is where your creativity really gets to shine, in a way, making each piece distinct. It's pretty satisfying to see your ideas come to life on the clay, honestly.
Remember that the clay is still quite delicate at this stage. It’s important to handle it with care to avoid distorting the shape you’ve just created. You might let it firm up a little, to a state often called "leather hard," before doing too much detailed work. This allows the clay to hold its shape better while you add your finishing touches. Once you're happy with the design, the piece will need to dry slowly and completely before it can be fired. Proper drying is a very important part of the pottery process, as it helps prevent cracking during the firing stage. Taking your time with these steps ensures that your pottery tray foam pressing project turns out just as you hoped, which is pretty much the goal, right?
What Can You Create with Pottery Tray Foam Pressing?
The possibilities with pottery tray foam pressing are quite wide-ranging, especially when you think about items that need a relatively flat base or a gentle curve. You can make all sorts of trays, from small ones for holding jewelry to larger ones for serving food. Think about platters for appetizers, or even decorative wall hangings that have a consistent thickness. My text mentions that the objects made are commonly useful ones, and this method certainly helps in creating those. You could make a set of matching coasters, or perhaps a unique soap dish for your bathroom. The consistency this method provides means you can make items that look very professional, even if you’re just starting out, you know. It really opens up new avenues for creative expression, honestly.
Beyond simple trays, you can also experiment with different shapes of foam to create more unusual forms. What about a wavy-edged dish, or a tray with multiple compartments? The foam can be cut or shaped to create specific contours, allowing for a good deal of customization. This means you’re not limited to just basic squares or circles. You could even combine foam pressing with other techniques, like adding hand-sculpted elements or attaching pieces made on a wheel. It's about using pottery tray foam pressing as a foundation for your creative ideas, building upon it to make truly unique pieces. The method is quite adaptable, which is one of its real strengths, so you can pretty much let your imagination guide you.
Tips for Better Pottery Tray Foam Pressing
To get the best results from your pottery tray foam pressing, there are a few simple tips that can help. First, make sure your clay slab is rolled out very evenly. Any differences in thickness can lead to uneven pressing and potential issues later on. Using a rolling pin with guides or a slab roller can really help with this. Second, ensure your foam is clean and free of any debris that could leave marks on your clay. A smooth, unblemished foam surface will give you a smooth, unblemished clay surface. It’s about paying attention to the small details, which often make a big difference in pottery, you see.
When you apply pressure, try to do it slowly and evenly across the entire surface. Don't just push down in one spot. Distribute your weight or the press's force to ensure the clay settles uniformly into the foam. This helps prevent air bubbles from getting trapped and ensures the clay is compressed consistently. After pressing, carefully remove the clay from the foam. Take your time to peel it away gently to avoid distorting the shape. Letting the clay firm up a little before you handle it too much can also be helpful. By following these simple suggestions, your pottery tray foam pressing projects will likely turn out much better, giving you pieces you can be truly happy with, which is the main point, right?
- Nina Agdal Naked
- Did Belle Gibson Ever Go To Jail
- Wyoming Murder Suicide
- Ella Mai Age
- Miley Cyrus Snl 50
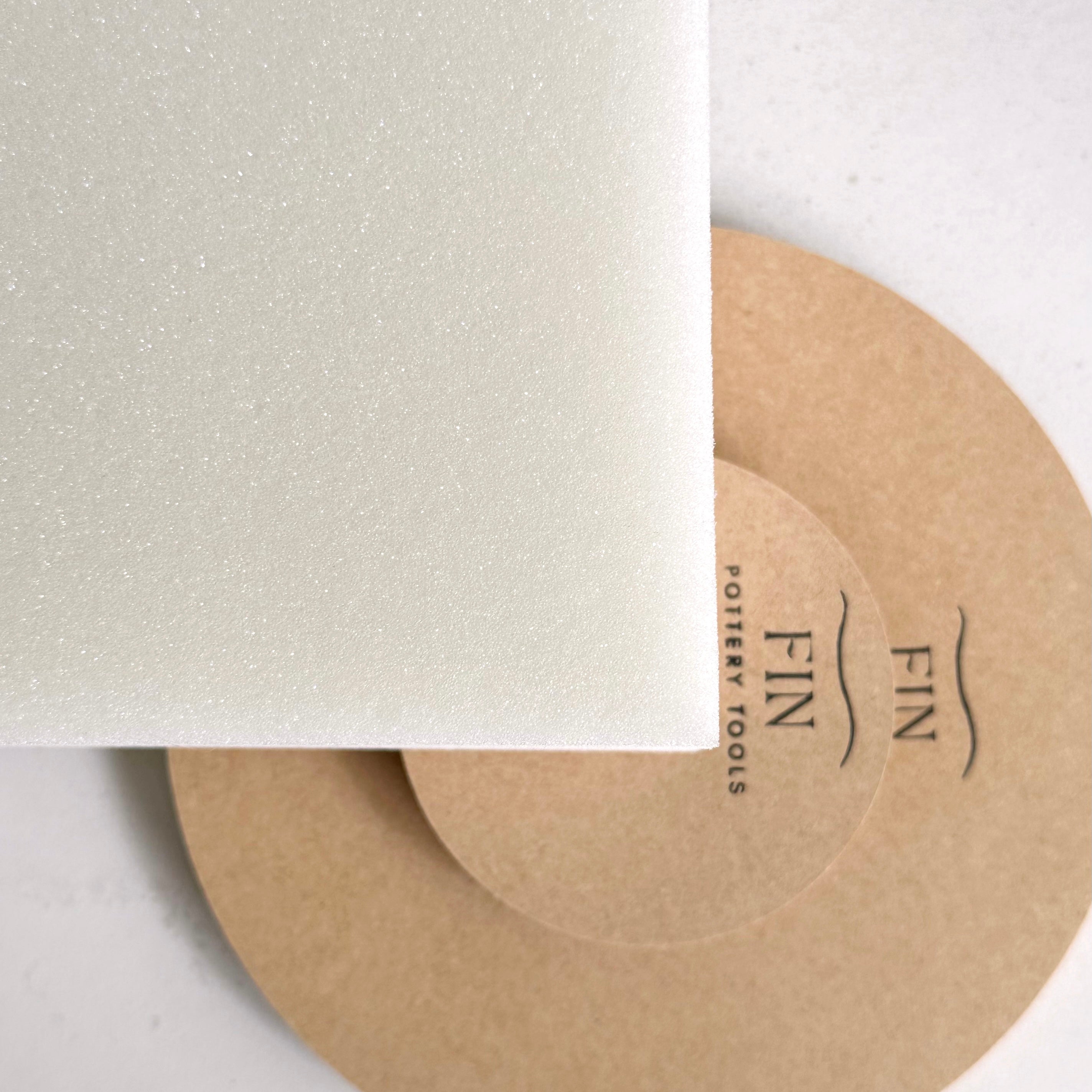
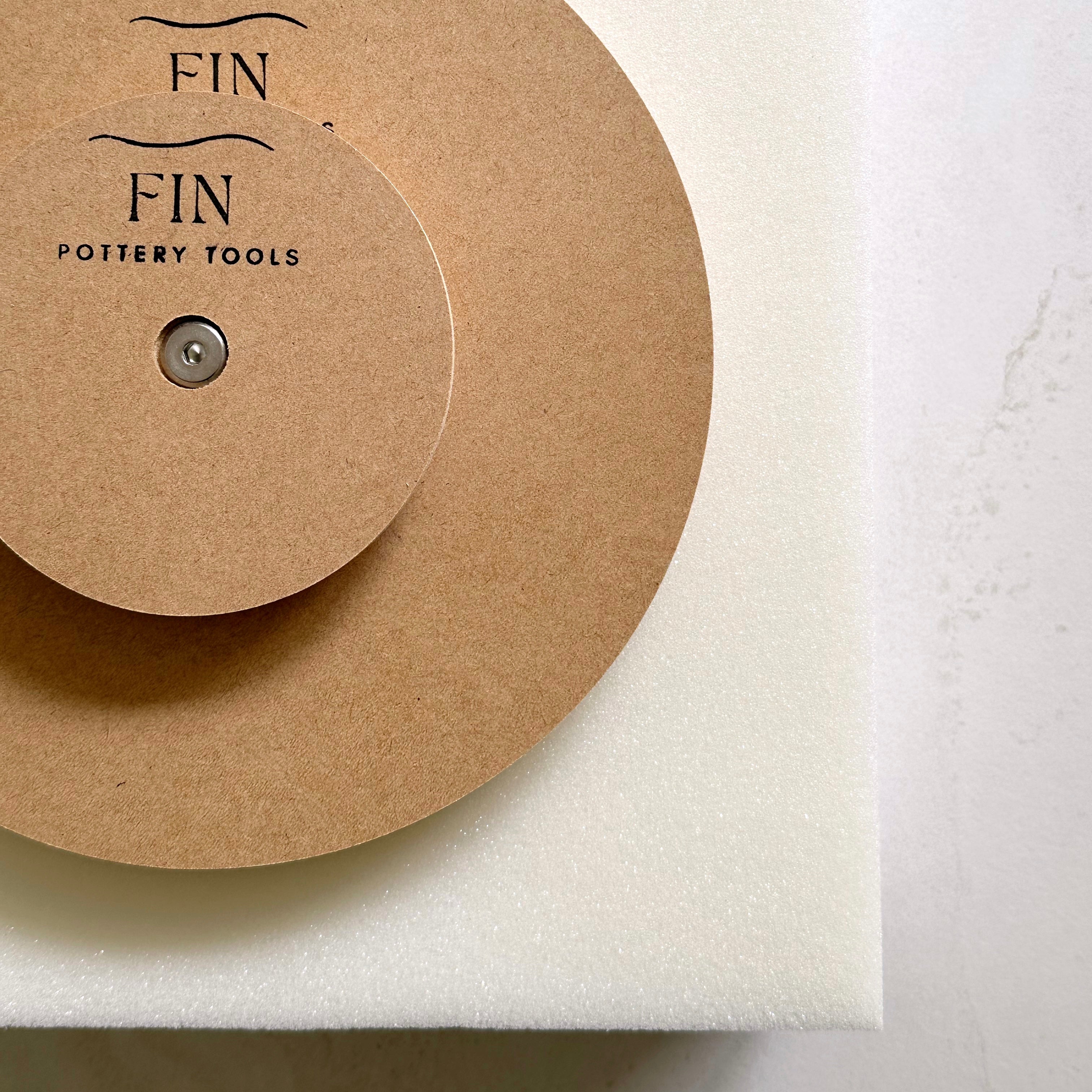
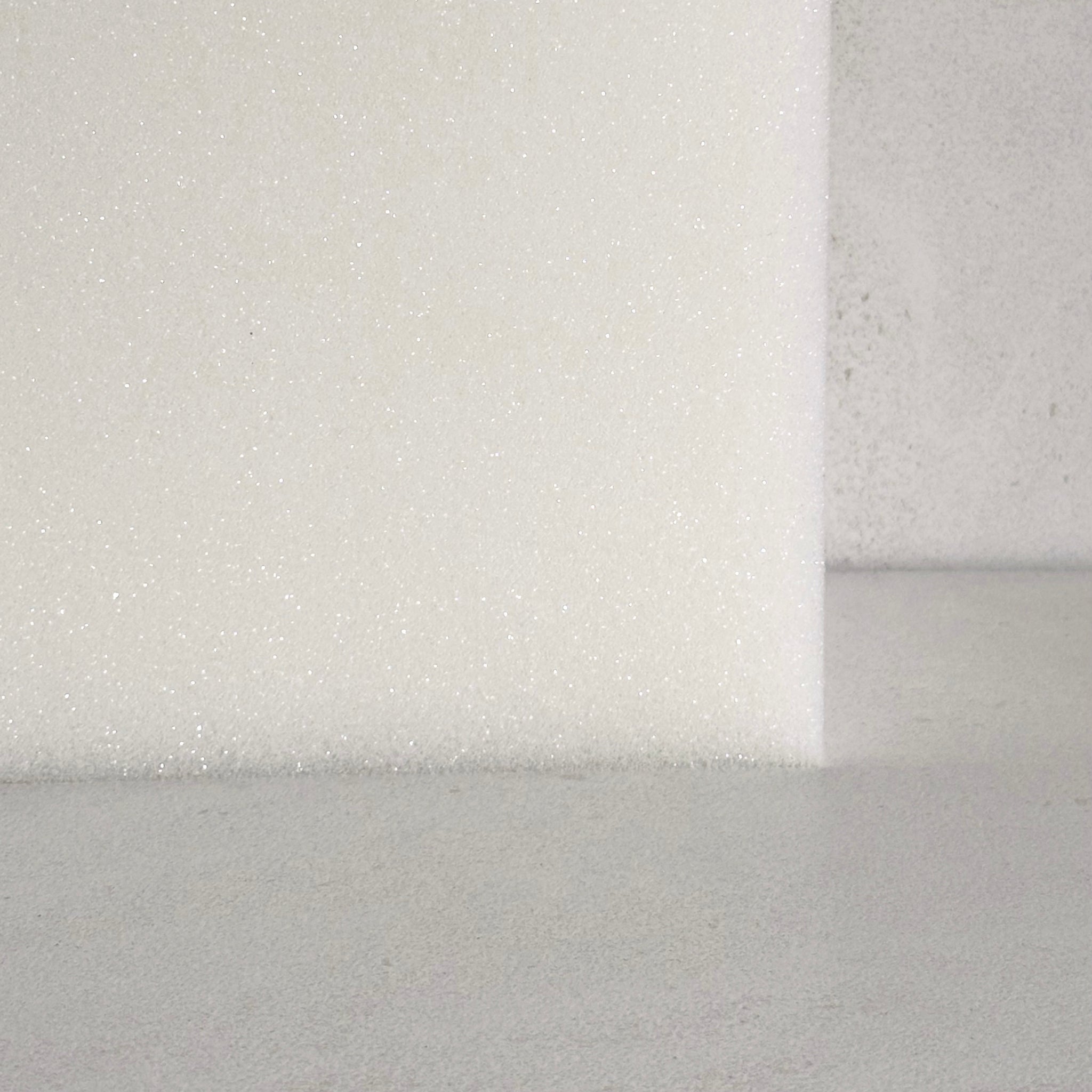